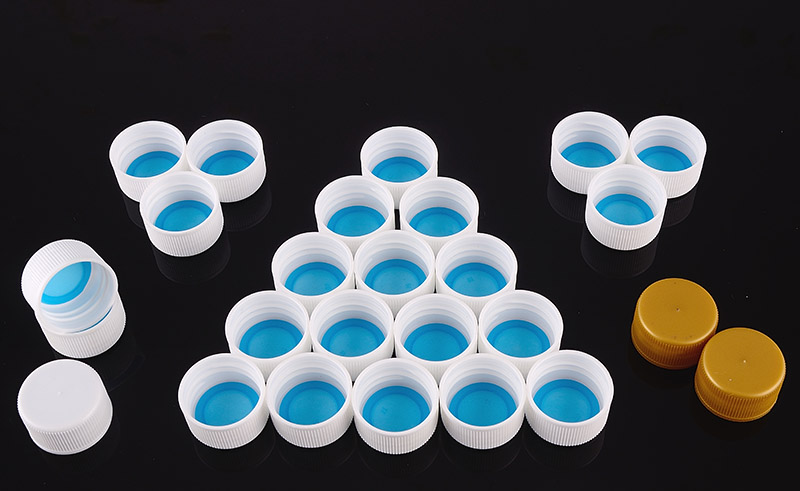
Manufacturing Process of Plastic Bottle Cap Molds: Precision Engineering for Perfect Seals
Plastic bottle caps are ubiquitous in packaging, and their quality hinges on the molds used to produce them. A bottle cap mold manufacturing factory combines advanced technology and meticulous craftsmanship to create durable, high-precision molds. Here’s an in-depth look at the process:
1. Design & Engineering
The journey begins with CAD (Computer-Aided Design) software, where engineers design the mold to meet specifications such as thread patterns, tamper-evident bands, and sealing surfaces. Key considerations include:
Core and Cavity: The two halves that shape the cap.
Cooling Channels: Optimized layout to ensure even cooling and reduce cycle times.
Ejection System: Pins or sleeves to safely eject caps without damage.
Draft Angles: Slight tapers to facilitate easy release.
Tolerances: Tight precision (often within microns) to ensure consistency.
Advanced simulation software predicts material flow and cooling, minimizing defects like warping or air traps.
2. Material Selection
Molds are typically crafted from high-grade steel alloys such as P20, H13, or stainless steel, chosen for their hardness, thermal stability, and resistance to wear. The material impacts the mold’s lifespan—premium steels endure millions of cycles.
3. Precision Machining
CNC Machining: Computer-controlled mills and lathes carve the core, cavity, and components with extreme accuracy.
EDM (Electrical Discharge Machining): Shapes intricate details (e.g., threads) using controlled electrical sparks.
Surface Finishing: Polishing or texturing ensures caps have the desired gloss or grip.
4. Heat Treatment & Surface Enhancement
To enhance durability, components undergo quenching and tempering, hardening the steel. Additional treatments like nitriding or chrome plating may be applied to boost wear and corrosion resistance.
5. Mold Assembly
Skilled technicians assemble components:
Aligning core and cavity within the mold base.
Installing ejector pins, cooling lines, and guide pins/bushings.
Integrating sliders or lifters for undercuts (e.g., tamper-evident rings).
Precision alignment is critical to prevent defects like flash or misaligned threads.
6. Testing & Validation
Trial Runs: Plastic (often the client’s specified material) is injected to produce sample caps. Engineers assess fill quality, cooling, and ejection.
Adjustments: Modifications to temperature, pressure, or cooling rates optimize performance.
Cycle Time Optimization: Balancing speed and quality for efficient production.
7. Quality Assurance
Dimensional Checks: Coordinate Measuring Machines (CMM) verify critical dimensions.
Functional Testing: Caps are tested for torque resistance, seal integrity, and compatibility with bottles.
Certifications: Compliance with standards like ISO 9001 ensures reliability.
8. Customization & Scalability
Factories offer tailored solutions, including:
Multi-Cavity Molds: Producing dozens of caps per cycle.
Hot Runner Systems: Reducing waste by maintaining molten plastic in the manifold.
Conclusion
The manufacture of plastic bottle cap molds is a blend of innovation and precision. From design to quality control, each step ensures molds deliver caps that seal securely, open smoothly, and endure rigorous use. By leveraging advanced technologies and expertise, factories uphold the stringent demands of industries ranging from beverages to pharmaceuticals, underscoring the mold’s role as the unsung hero of packaging.